Beyond the Customary Dimensions.
Around 700 kilometers of power lines were laid, a supply of up to 24 megawatts, and two-story air handling units the size of a family home. It only takes a few words to get a feel for the scale of this project. In fact, the modern production hall in Graben-Neudorf, Baden, is a new factory building with almost gigantic proportions. robatherm has equipped the finished plant with customized ventilation and air handling systems.
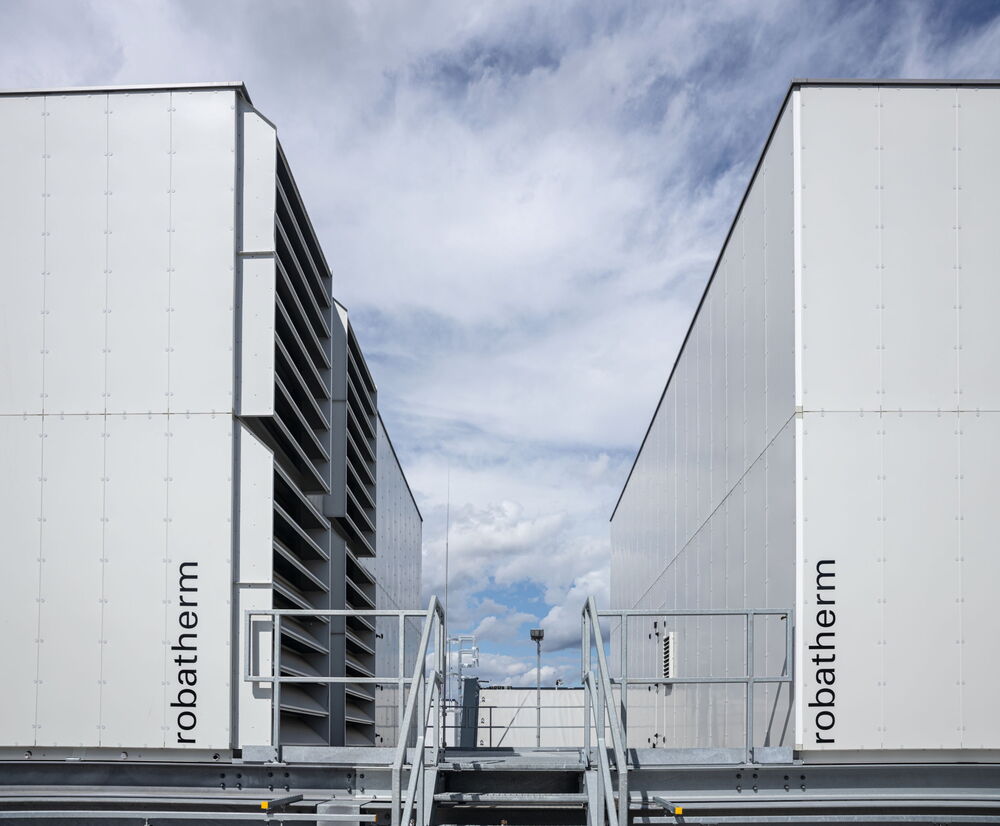
SEW-Eurodrive is a renowned global player for electric drive technology covering a wide range of applications. A state-of-the-art „Smart Factory“ was created in the North Hall to expand its capacities for the future. The complex comprises all areas, from the incoming goods department to the distribution warehouse, production, packaging, and office space. The results are modern geared motors, gear wheels, shafts, and rotors for the global market. One key ecological driver is the building‘s photovoltaic system: With a maximum output of around 2.5 MWp from solar energy, it reduces CO2-emission rates by over 1,550 tons per annum.
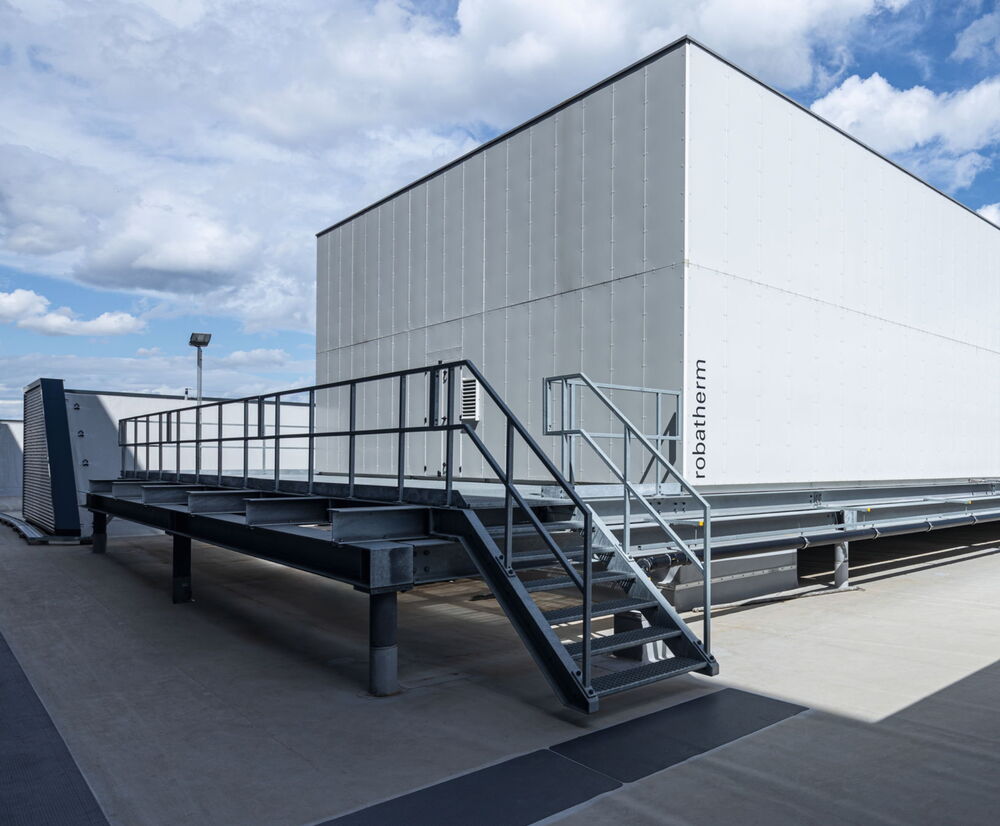
Familiar terrain in new dimensions.
The air handling technology had to be dimensioned accordingly to accommodate the factory size. SEW-Eurodrive is by no means new terrain for robatherm. SEW-Eurodrive had already been equipped with individual air handling solutions by the „air handling company“ for several projects in Bruchsal and Graben-Neudorf. However, in this case, other framework conditions existed regarding dimensions, logistics, and technology.
A realistic 3D visualization of an air handling unit was created during the planning phase to grasp these dimensions early. The detailed rendering allowed the project planners to navigate virtually through the unit in advance. „This made it possible to visualize the intricacies of the AHU concept in the best possible way,“ said Michael Birg, praising the resulting transparency. As Managing Director of ID Ingenieurbüro Dresen & Birg, he was responsible for planning the entire building technology.
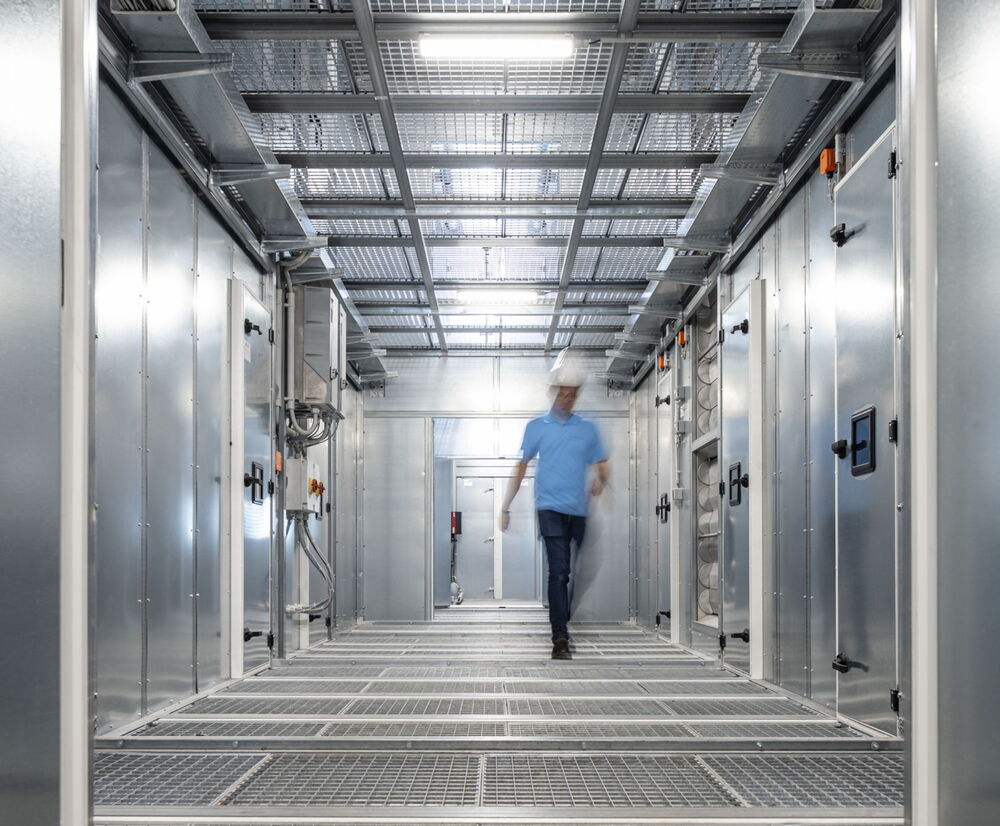
Air handling units the size of a residential house.
robatherm delivered a total of 28 air-handling units for this new building. Together, they produce a total air volume of 1,612,000 m³/h. Their sheer physical size is also impressive: Each of the 15 weatherproof units, mounted on steel platforms, is almost
20 meters long, around 10 meters wide, and
4.50 meters high. All two-story air handling units have a roomy split level in the maintenance aisle, through which all components are quickly and conveniently accessible. Airtightly separated by doors, this corridor can also be used as a bypass. The energetic advantage of this option is that temporarily unused components - such as the air cooler and re-heater in winter operation - can be circumvented via the bypass to reduce pressure loss.

Precise and efficient air conditioning.
Since electronics and gearbox production require special indoor air conditions, the properties of the AHUs were precisely tailored to these conditions. The indoor climate requirements here fall within a narrow tolerance range.
robatherm‘s solution has a lot to offer: The air dehumidified by cooling in summer is then reheated by a re-heater to achieve the exact temperature and humidity. Because the air handling units also extract the exhaust air from the production machines, metal filters and an external motor ventilation system were installed. The heat recovery system was based on high-performance run-around coil systems (RAC) to minimize potential cross-over of polluted air. In addition, all the stainless steel piping and all control groups were planned three-dimensionally before implementation. The pipework insulation was then encased in galvanized sheet steel.
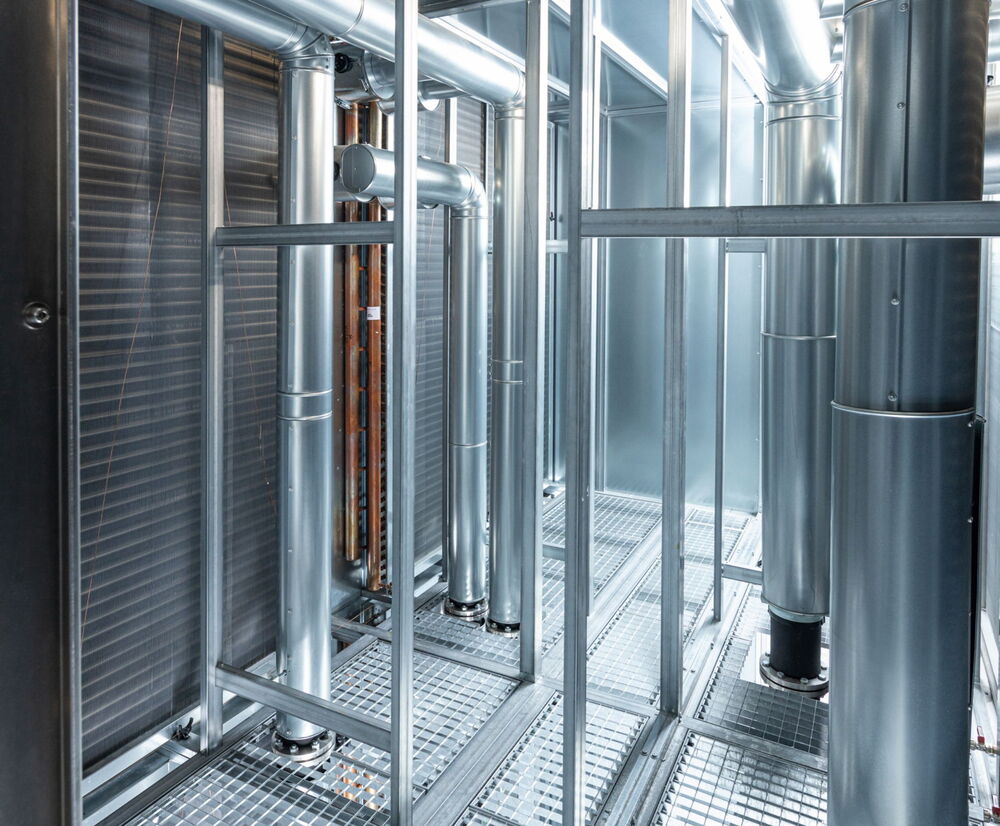
All levels synchronized.
The project called for optimally coordinated planning. „Close cooperation and reliable coordination on all levels are crucial to managing a project of this size.“ This is how Michael Schlindwein, Managing Director of Schlindwein Anlagenbau, gets to the heart of the matter. He was responsible for the building technology installation. He emphasized the significance of intensive exchange between plant engineers, the planning office, and robatherm. Throughput times were defined so tight time frames could be consistently maintained. After all, the air handling units had to be packed at robatherm in weather-protected packaging and loaded on time. In light of the enormous dimensions, the units for SEW-Eurodrive could only be stored temporarily at robatherm. Production deadlines and delivery dates had to be closely coordinated.
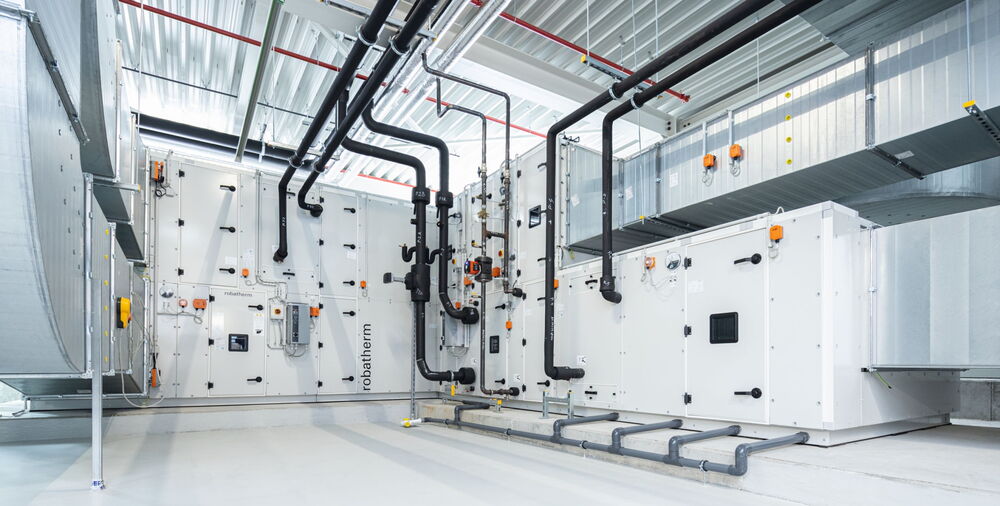
Logistically challenging.
All air handling units were to arrive for installation at SEW-Eurodrive as late as possible, ideally Just-in-Time. On the one hand, only limited space was available at the construction site for temporary storage. On the other hand, construction progress must not be delayed by late deliveries. The total of 326 truckloads from robatherm to SEW-Eurodrive alone is a perfect symbol for the logistical challenge. Thinking ahead and thinking bigger - these were the
project‘s defining factors. And the result is impressive.
The dimensions become particularly clear in the video.